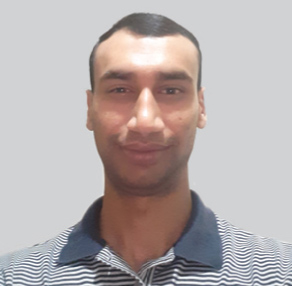
In an integrated pest management (IPM) programme, irrigation management is viewed as an essential component where dryland plantings are not feasible. Numerous scientists note the importance of adequate, timely irrigation to prevent unnecessary stress to crops so that they are better able to withstand pest pressure.
Standing water, for example, hinders the growth of crops. In addition, root diseases and nematode infestations are generally the result of poor water infiltration or lack of drainage. Therefore, irrigation management will affect diseases, insects, rodents, and weeds. While this is not new information, the question is whether irrigation can be directly utilised to manage pests. The answer is yes. Irrigation methods in pest management include: (1) flood irrigation; (2) high-pressure water spray and, most notably; (3) chemigation.
Flood irrigation and high-pressure water spray
Flooding of fields is usually recommended for minimising attacks from pests such as cutworms where one or more life stages are passed in the soil. The flooding operation results in water permeating through the soil pores where the soil-inhabiting stages of the insect are suffocated. In general, high-pressure water sprays are utilised to dislodge spider mites, aphids, small caterpillars, and various other pests from the host plants. This method has long been considered a non-chemical method of pest control.
‘From a commercial perspective, flood irrigation and high-pressure water sprays will not replace the need for pesticides,’ notes Dr Jeremy M Goodall of the Agricultural Research Council (ARC).
Chemigation
Chemigation is the process of applying an agricultural remedy – in this case a pesticide – to the soil or crop foliage, using an irrigation system as a conduit where the pesticide formulation is metered into the irrigation water via an injector at the pump station on the crop end. Based on the type of pesticide applied, chemigation may be referred to as herbigation (herbicides), insectigation (insecticides), and fungigation (fungicides). Benefits to producers include the following:
- The method is considered to be accurate, particularly when numerous applications are required in a growing season.
- Activation of moisture-dependant pesticides.
- Obstacles such as wet soils or tall crops where access is an issue, are eliminated.
- Corrective measures can be implemented timeously.
- Reliance on mechanisation is reduced, which saves on fuel costs and reduces soil compaction.
- Little mechanical damage to crops when compared to other ground apparatuses.
- Reduced risk of operator exposure.
However, for the benefits to be realised, there are several considerations for producers before deciding to choose chemigation. Key considerations include the following:
- Producers will have to seek the services of a qualified professional to design, install and commission the injection system, where repair, maintenance and operational costs over time must be taken into account.
- It requires regular calibration of the application system to ensure correct product label application rates.
- In the case of centre pivot and overhead sprinkler systems, corrosive damage to pipes may occur when incorrect chemical carriers are utilised.
- Employees will have to be well trained to maintain and proficiently operate the irrigation system and injection apparatus.
- Contamination risk to the water source resulting from poor backflow control of pesticides into the water supply, thereby presenting a potential environmental pollution risk.
- Longer application in comparison to other application methods.
- Possibility of equipment malfunction when employees are not present at the application site.
- A great deal of dependency on distribution uniformity of the irrigation system to ensure product efficacy and crop safety.
- The additional cost of installing and maintaining anti-pollution devices.
- Wind, heat, and evaporation may affect application volume and uniformity, particularly with overhead irrigation systems.
- The general rule of thumb for overhead sprinkler systems and centre pivots is that chemigation must not be conducted where wind speeds exceed 15 km/h.
- High temperatures and low relative humidity will increase evaporation of water/pesticides.
Irrigation systems
An irrigation system in good working order with responsible irrigation management is required for chemigation to be successful. The specifications of an irrigation system will determine not only the type of pesticides that can be applied, but also the injector type, rate, and duration. In-field evaluation of irrigation systems will be crucial to ensuring the system conforms to acceptable performance levels in terms of flow rate, operating pressure, and uniformity in distribution prior to chemigation. Micro-sprinklers, drip, portable, semi-permanent and permanent systems (i.e., static irrigation systems) irrigate fields at a constant rate. Drip and sprinkler systems are widely considered as improved irrigation versions with advantages. Precise and adequate water supply aimed at the root zone resulted in these technologies being acclaimed worldwide. Moving systems such as pivots and linear systems, on the other hand, encompass variable application rates which require the injection rate of the pesticide to be synchronised with running speed.
While chemigation can deliver significant returns on investment, it needs to be correctly implemented. This will largely be determined by the choice of equipment utilised. Given the real possibility of loss of income due to crop and equipment failure, producers must only use suitable equipment while not compromising on quality.
Application methods
Currently there are three types of injector methods. While the information and detail here are beyond the scope of this article, the methods are briefly described. Firstly, a passive apparatus utilises energy already available within the irrigation system (i.e., water from pump) or atmospheric energy to inject an agrochemical into the water. Secondly, an active apparatus utilises an external source of energy (i.e., electricity) to inject an agrochemical into the water. Finally, a combination of both the methods mentioned, where the injection pump is powered by energy within the pipeline together with an external source.
Chemigation and pesticide product labels – why this matters
- Chemigation can be applied only if the product label allows such application and only according to the label directions and restrictions. In other words, labels must specifically state that the product can be applied through an irrigation system.
- Labels provide specific mixing, application, and safety precautions.
- Producers are reminded that the label of a pesticide product is a legal document under the Fertilisers, Farm Feeds, Agricultural Remedies and Stock Remedies Act, 1947 (Act No. 36 of 1947).
- Where a pesticide label states nothing regarding chemigation, the product must not be applied in that manner.
- Currently in South Africa, there are only a few examples of pesticide products that allow for chemigation. Producers wanting more information in this regard should consult with their crop advisers.
- Take note of any specified safety devices listed on the product label for the irrigation system and injection apparatus.
- Certain labels may specify how often the chemigation system must be monitored.
CropLife SA’s advice to grain producers
When selecting a pesticide for application through a centre pivot irrigation system, grain producers must ensure that it is registered for such use – this the first and most critical step in the decision-making process. With that said, additional factors cannot be ignored:
- The system should not be near occupied buildings/dwellings, sources of surface water, neighbouring crops, and roads.
- The operation must not pose a danger to people, animals, and non-target sites.
- It is no secret that soils can vary over short distances and, therefore, the infiltration rate will vary according to the type of soil.
- Field topography can influence uniformity of application through centre pivots due to the absence of suitable sprinklers.
- Terrain differences will result in pressure differences at different nozzle outlets, leading to uneven water distribution. However, this can be corrected by utilising pressure regulators for each sprinkler.
- The characteristics of pivot irrigation systems can affect the capacity for applying agrochemicals. Centre pivot sprinkler irrigation systems may be used to apply pesticides which have to be incorporated into the soil when foliar application is required.
- Any machine used for chemigation must have appropriate anti-pollution safety devices installed. This ensures operator and environmental safety together with the desired results of the pesticide application.
- Drift, together with runoff, are the leading causes of inadvertent losses resulting from pesticide applications.
- As touched on earlier, if the wind is strong (>15 km/h), the system must be shut down to avoid off-target application.
- Runoff becomes a possibility when the system applies water at a rate higher than what the soil can absorb. This is influenced by: (1) slope; (2) roughness of soil surface; and (3) presence of a crop canopy or residue. Runoff in this context presents a hazard to surface and ground water resources, livestock, adjacent crops and wildlife. Adjust the amount of water being used to apply the pesticide in order to prevent runoff.
- Correctly calibrating the application system remains vital. This will ensure that the correct amount of pesticide is applied. Overapplication is wasteful expenditure and may result in prosecution for misuse, whereas underapplication will not yield the expected outcomes.
Final word
It should now be clear to producers that chemigation requires thorough understanding and investment. In particular, the high demands relate to training, skills, handling, setting up, maintaining and calibrating equipment. In this regard, an expert should be consulted when considering chemigation. Like other methods of pesticide application, safety remains the primary concern, where potential hazards must be assessed and minimised as best as possible. Lastly, pesticides utilised must be consistent with the product label at all times – take note of the registered methods of application.