This article aims to cast some light on the workings of the South African Grain Information Service (SAGIS) – specifically the inspection department – and how SAGIS verifies its data to ensure the most accurate information is provided to the industry.
Any market participant that imports and exports or handles grains and oilseeds commercially is statutorily compelled under the Marketing Act of Agricultural Products (Act No. 47 of 1996) to register with SAGIS and submit information.
SAGIS was established in 1997 by the industry and is therefore also reporting on what the industry requires to function in a free market system.
Various weekly and monthly data are made available for nine different grains and oilseeds as listed in Table 1 to 3.
The accuracy and therefore the quality of data supplied by SAGIS to the industry is dependent on the correctness and timeous submission of returns. Returns submitted on time allow SAGIS the maximum time to verify and reconcile data more accurately. From Graph 1, it is evident that co-workers do submit their returns with an average of 99,7% total submission over the past five years, with an average of 73,3% submission being on or before the 10th of a month. SAGIS does experience challenges with some late returns, but generally have good cooperation.
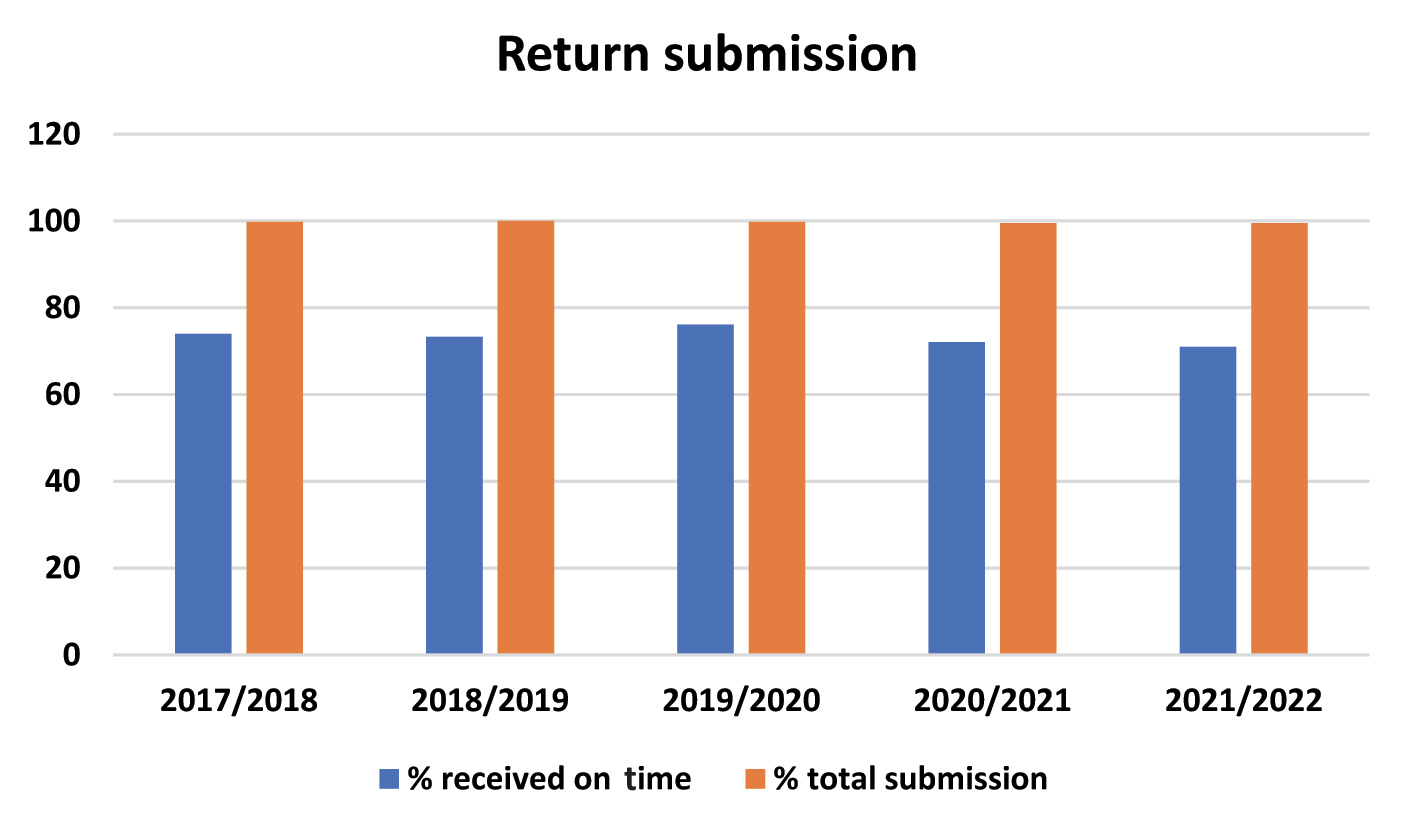
Data processing
As soon as returns are submitted, the various processes with regard to reconciliation, validation and balancing are started.
SAGIS reports on the movement of grain, which includes reporting by co-workers of what they receive and dispatch from and to premises.
The dispatches and receipts are then reconciled with one another, and differences are followed up with co-workers to obtain answers. Differences could include stock in transit which must be included to ensure that the most accurate stock levels are reported. These reconciliations will also ensure that the most accurate producer deliveries are declared.
Stock declared on the returns is also compared to a co-worker’s available capacity and then queried when it is exceeded.
Additional external sources are used to ensure that the different types of data available in the industry correlate with one another. This includes SARS import and export tariff lines and Transnet data on rail transits. Import and export vessel capacities are checked against actual declarations to ensure that there is no duplication by exceeding a vessel’s capacity.
Internally the product and weekly data received from co-workers are also compared and reconciled with the monthly whole grain data to try and identify any errors on returns. Various datasets provide personnel with historic trends and highlight any set of data outside the norm. ‘Own premises’ returns are reconciled with ‘not own premises’ returns to ensure that all trader data are confirmed by the physical premises and to ensure that traders are declaring all import and export data.
Grain or oilseeds sold to end consumers and withdrawn by producers are investigated to ensure the tonnages are declared under the correct return item. Producers’ withdrawals are investigated to ensure they are not duplicated if that same producer withdraws from a silo and delivers at a miller and whether end consumer data should not be declared under animal feed, for example.
Inspections
The SAGIS info and inspection teams are constantly in communication regarding any queries and non-compliant co-workers throughout the whole process. This ensures that questionable data are investigated as soon as possible, and non-compliant co-workers are treated with the necessary attention. The aim of the inspection team is to do an inspection at every co-worker’s premises once a year.
As can be seen from Graph 2, the Covid pandemic did influence SAGIS inspections when travel restrictions were put in place and various co-workers had limited access to only the most necessary people. During the 2020/2021 and 2021/2022 financial years the option of electronic inspections was explored. However, even though there were certain benefits in doing this, physically counting stock was impossible. As soon as travel restrictions were lifted, SAGIS continued on-site inspections as it was very important to ensure that correct data were received and to physically verify stock levels.
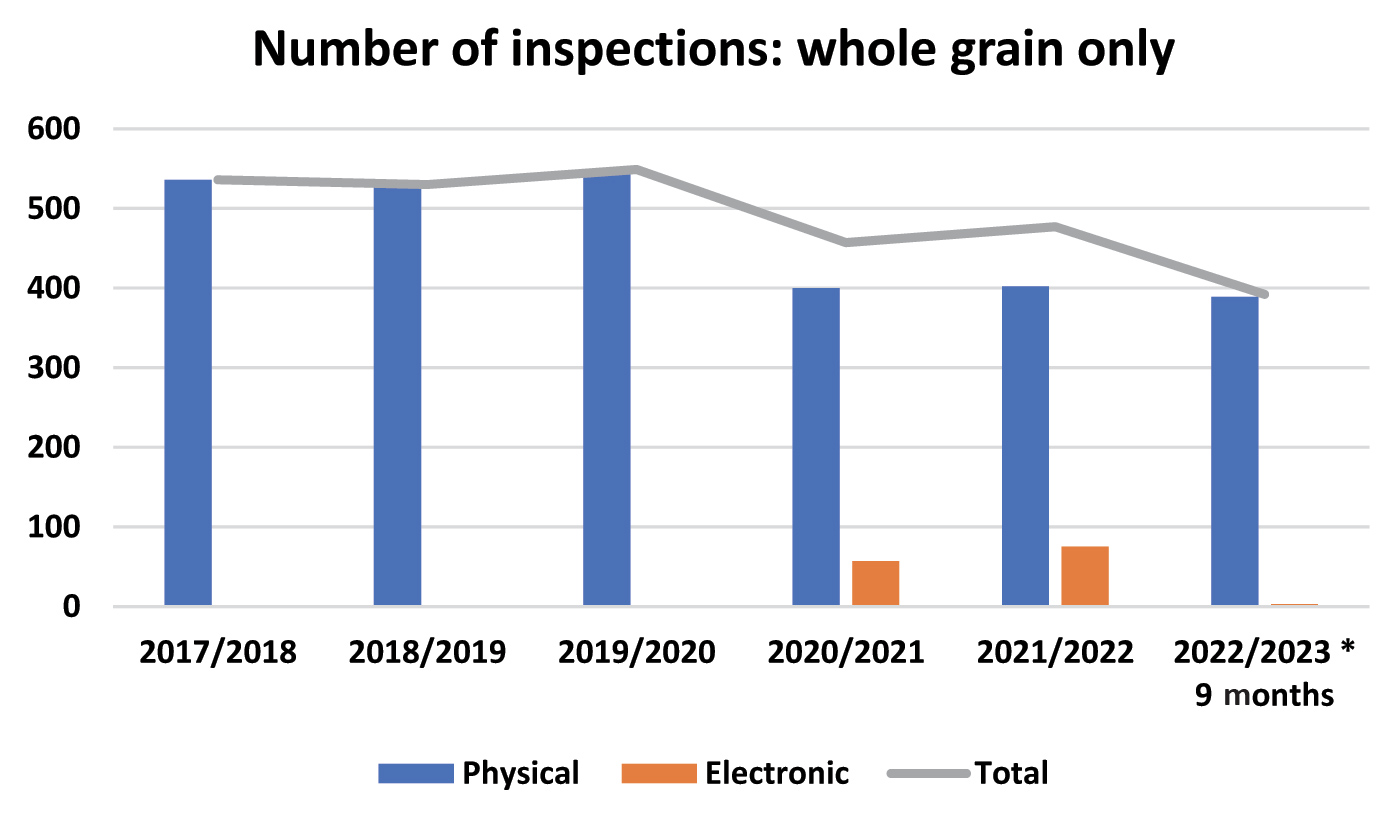
During an inspection, source documentation is compared and verified with the data supplied on the return. A physical stocktake also takes place to verify stocks on the premises.
Co-workers who require training in the completion of returns or who have been identified as a risk are a priority for the inspection department. Out of sequence or urgent visits are made to such co-workers to ensure SAGIS receives the correct data. Inspectors also keep an eye open in the surrounding areas where they do their inspections to ensure any new firms are identified or registered and make sense of the data as supplied by the co-worker.
Once an inspection is finalised, the senior management of the co-worker will receive a feedback letter with regard to the inspection. The results from these inspections are summarised in Table 1 to Table 3.
Table 1 represents the total amount of receipts audited on inspection. This includes receipts directly from farms, harbours, border posts and other South African premises. From March to November of the 2022/2023 financial year a total of 19 135 838 tons were audited with immaterial differences overall as can be seen on the right of the table.
Table 2 consists of the stock physically counted by SAGIS inspectors. The methods being used depend on the structure they encounter. Stock is physically measured and the tonnage is then calculated according to the structure’s dimensions/volume. A co-worker’s movement is then used to recalculate the stock back to the last return’s declaration. For the current financial year, 4 827 711 tons of stock were physically counted.
Table 3 indicates the stock percentage overdeclared or underdeclared for each financial year. Once again, all differences were within acceptable norms.
The current inspectors at SAGIS have the required knowledge and experience to perform their duties accurately. The experience gained include Maize Board experience of 13 years, Wheat Board experience of ten years and a combined 55 years’ experience within SAGIS.
Non-compliance
A co-worker that does not adhere to the requirements of the statutory measure is guilty of an offence and can be prosecuted.
Certain steps and procedures are followed internally to try and create corrective action with a co-worker where management is actively involved with these co-workers. There have, however, been cases where internal actions were not successful in, for example, obtaining outstanding returns. The necessary legal steps were taken and no court actions have had to take place up to date.
In the case of incorrect data supplied, an investigation will determine whether it was negligence or lack of understanding. In the latter case, proper training will be supplied to the person completing the returns and arrangements will be made with the co-worker to ensure the correct data are supplied to the person completing the returns. Should it be negligence or a material breach, the senior management of the specific co-worker will be contacted, with a written explanation required. Corrective measures are put in place to prevent this from happening going forward. A continuous disregard for the accuracy and correctness of returns will result in the matter being handed over to SAGIS’ legal representatives.
SAGIS has experienced a cooperative and understanding relationship with its co-workers over the years and hope to build on that and continue to serve the industry with reliable data.