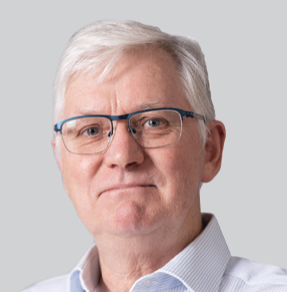
Strategic Projects, SAPIA
There is a story about a technical assistant at one of the major oil companies who was called out by a producer who complained of diesel contamination which was affecting the operation of his machines. The technician dutifully made his way from Johannesburg to the farm and travelled down a dirt road towards the diesel storage area, where he found a horizontal drum atop a structure allowing the producer to gravity feed his machines. On approaching this structure, the technician immediately turned around and drove back to his office.
After witnessing this, the annoyed producer phoned the technician’s manager to complain about what had happened. When questioned, the technician replied that there was no problem with the fuel – the producer was the problem. He had wasted his time travelling halfway across the country to attend to a problem which was of the producer’s own making. He had propped up the structure on one side to ensure all fuel would drain towards the outlet – this sounds logical to maximise the use of available diesel. However, the design of these drums is such that the fuel outlet is situated some way off the base so as to allow any water in the fuel to settle to the base of the drum so that water-free diesel can be dispensed to equipment. The producer’s actions had, in effect, negated this design consideration, allowing any water at the bottom of the drum to be dispensed into the equipment with the diesel.
This episode illustrates a number of issues: the design of fuel-handling equipment; the importance of product knowledge; and related to this, basic housekeeping and cleanliness.
All these aspects work together to deliver fuel that should be fit for purpose and provide peace of mind to the consumer of the product. Regulations and standards are put in place to provide for the consistency of product, what is required of the manufacturers of fuel and related equipment, and protection in terms of safety, health and the environment.
Product knowledge is important, especially with respect to those aspects of the product that are in control of the final user. Specifications and standards are put in place to control aspects out of the immediate control of the consumer and to ensure products of consistent quality. These standards are reviewed periodically to keep up with technological developments and to ensure fit-for-purpose fuels.
Housekeeping and cleanliness are closely related – as illustrated in this example, water was the issue. However, it extends to wider product integrity aspects which include dirt, microbiological growth and adulterants. Moreover, there are other factors such as viscosity, sulphur content, lubricity and cetane which can affect performance in use. These factors can affect the reliability and longevity of machinery. Oil companies go to extraordinary lengths to ensure that diesel delivered to their consumers satisfies all the requirements associated with the local diesel standard – SANS 342 – and more.
Visual inspection
For the average consumer many of the parameters provided in SANS 342 are beyond their control and can only be determined from laboratory testing. Therefore, only visual inspection of the fuel can provide an initial assessment of fitness for use covering three main areas – appearance, the presence of water and the presence of dirt.
Appearance
An initial assessment of the fuel must show that it is bright and clear. This means that the fuel must be translucent and clear of any contaminants such as water or particulates. Undyed diesel is normally a straw colour or light greenish yellow, but can be ‘water white’ – looking like water. Some, but not all companies, dye their diesel blue or purple which is indicative of the grade of diesel – blue indicates a maximum sulphur content of 50 ppm (w/w) while purple indicates 10 ppm (w/w). In all cases it must be possible to see through the fuel without noticing any particulate matter or water droplets present in the fuel.
It should be noted that during cold weather the fuel may not be bright and clear, but could be cloudy due to the presence of waxes that have precipitated from the diesel because of the cold. This is a natural occurrence and when the fuel heats as the weather warms, the waxes will redissolve and the fuel will become ‘bright and clear’. This process is accelerated when the engine is started and warmed by passed fuel that is returned to the tank.
Presence of water
Water, the issue affecting our producer’s story above, causes corrosion, but also reduces the ability of the diesel to act as a lubricant. Diesel itself contains very small amounts of water from its production, but it is normally fully dissolved into the product when it meets the SANS 342 standard. However, if additional water is introduced into diesel through the supply chain by whatever means, it may drop out of the diesel when it becomes cold and then present itself as free water.
Modern engines have sophisticated water filters to minimise the amount of water passing through to the engine, but even these have operability limits and water can break through if present in sufficient quantity in the fuel. Furthermore, non-approved additives can also deactivate the water separator filter, thus limiting the ability to prevent free water from entering the fuel injection system, exacerbating the problem. Over time this water causes corrosion of the fuel system, affecting fuel lines and injectors. Corrosion products can block injectors which are manufactured to very fine tolerances and will lead to incorrect fuel delivery into the cylinder in terms of both volume and spray pattern, resulting in increased consumption. Eventually the injectors will fail and will need replacement. It is thus obvious that water management is critical to machine operability, fuel consumption and the lifespan of equipment.
Oil companies take extraordinary measures to ensure the integrity of their logistics systems to minimise or eliminate the introduction of any water into the fuel. Consumers themselves can take measures to reduce any water introduced after delivery. This can be done by ensuring that fuel storage and dispensing equipment are placed in areas where the unwanted ingress of water is avoided, such as storm water run-off into underground tanks and the draining of low points in above-ground storage and distribution systems. Best practice further includes the regular inspection and draining of storage tanks and drums, ensuring inlets are sealed and that vents operate correctly. It is imperative to regularly check these systems to ensure that water cannot enter.
Presence of dirt
Dirt in diesel comes from a variety of sources, including dust, poor storage systems that include faulty tank venting, corrosion products from tanks and vessels and poor housekeeping of distribution systems which include pipelines, transfer lines, trucks and storage tanks. The presence of dirt is measured by total contamination for which the standard (SANS 342) provides for the maximum amount of particulate matter at 24 mg/kg of fuel.
The presence of particulate matter in diesel can block fuel filters and is a source of abrasive material that may cause wear and damage to the components in the fuel system, such as pumps and injectors – with the same outcomes as provided above.
It is obvious that good housekeeping measures are necessary to ensure cleanliness of systems handling fuel and to prevent the ingress of dirt into these systems. This would include periodic inspection to ensure such cleanliness.
Bacterial contamination
As mentioned above, diesel does contain a trace amount of water, but more may be introduced through the supply chain or in storage. This can happen from water present in the atmosphere that is absorbed into diesel during storage, or from condensation on the inside of tanks and/or from water leaks. Over time water may accumulate in sufficient quantity to drop out of the diesel and settle at the bottom of the storage vessel.
Water at the bottom of a tank will create an interface between the water and the diesel where bacterial growth can occur. However, the possibility of this occurring is dependent on the time spent in storage and the quick turnover of tanks will mitigate against potential bacterial contamination. Nevertheless, the introduction of biodiesel into the diesel pool may exacerbate the risk of bacterial contamination as biodiesel contains numerous fatty acid compounds upon which bacteria and fungi thrive. The introduction of biodiesel blends is gaining increasing focus as a way to decarbonise the fuels pool in the fight against climate change. Furthermore, the increase in imports of diesel over the years may result in contaminated diesel from ships being discharged into shared logistic systems.
Only a small amount of free water is necessary to allow for microbial growth. If this occurs, it will give rise to the formation of sludge and slime. These can block filters and nozzles and cause corrosion of fuel systems in machinery and the containment vessel from the organic acids formed by microbial action.
Treatment normally requires the use of approved biocides to kill the contaminants, but it is obviously important that the biocide used must be compatible with the fuel and all system components and not alter the properties of the fuel itself. At some stage a decision will need to be made regarding cleaning of the tank to remove any residual slime and sludge as a result of the contamination.
Diesel adulteration
Of major concern at present is the adulteration of diesel with illuminating paraffin. Entities blending paraffin into diesel seek to profit from the duties and levies administered on diesel which are not administered on paraffin. During 2023 these duties and levies amounted to approximately R6/ℓ, providing a healthy profit for any unscrupulous operator.
It should be noted that the blending of paraffin into diesel outside a licensed manufacturing warehouse at any level is illegal and if detected is subject to sanction. Oil companies mark their paraffin with a South African Revenue Services approved tracer (also called the A1 marker). If this marker is detected in diesel fuel above 1 mg/ℓ, then the inference is that the diesel has been illegally adulterated with paraffin. However, despite the use of this marker, the incidence of adulteration has ballooned over the past years with reported sales of paraffin more than doubling since 2017.
The blending of paraffin into diesel has a number of deleterious consequences to machinery and storage systems:
- It can reduce the flash point of diesel to below the maximum allowed (55 ˚C), increasing the risk of fire around facilities designed for diesel storage but now handling products with increased volatility.
- It will reduce the viscosity of diesel which can have disastrous effects on both fuel pumps and injectors.
- The lubricating action of diesel will be compromised. This will affect injector performance, resulting in incorrect fuel delivery and spray patterns to cylinders, leading to increased fuel consumption, noisy operation and the formation of black smoke.
- Injector failure can occur, which can also result in engine failure. Engine failure occurs if the injector fails in the ‘open’ position, meaning the continued dribble of diesel onto the cylinder head, causing piston crown failure as the fuel burns on the crown itself.
- It can lead to decreased power if the injector fails in the ‘closed’ position – effectively taking one cylinder out of operation.
- The cetane number of fuel will be reduced, providing for slower starting and noisy operation.
- It can increase the sulphur content of the fuel, which may result in black smoke production from tail pipes.
The detection of adulterated diesel by a layperson is very difficult, if not impossible. Only laboratory testing will ascertain whether the diesel has been adulterated or not. Apart from testing for the A1 marker, adulteration can also be detected via testing for viscosity, sulphur content and distillation.
For the layperson, the following symptoms may be indicative of paraffin adulteration:
- Engines will be slow to start.
- Noisy operation of equipment.
- Lack of power.
- Increased fuel consumption.
- A heavily discounted diesel fuel price due to the seller escaping the duties and levies of the paraffin blended into the diesel.
If this occurs, it would be prudent for the consumer to contact their supplier to enquire further as to what remedial measures may be undertaken.
Conclusion
To operate as designed, engines rely on the quality of fuel supplied to meet the prescribed standard – SANS 342. The increased sophistication of diesel machines and the proliferation of diesel adulteration have meant that consumers really need to pay heed to delivered fuel quality as well as to price. Without these considerations, the wear and breakdown of components could be anticipated, leading to costly repairs and downtime.
To mitigate against these effects, there is an increased requirement on the bulk consumers of diesel to pay extra special attention to their deliveries and to the housekeeping at their storage systems. Systems and procedures should be considered to reduce the risk of contamination and to ensure that fit-for-purpose fuel is used. Your diesel supplier should be in a position to advise you of such systems and procedures.
Acknowledgements: Southern African Institute of Tribology and South African Petroleum Industry Association Fuels Technical Committee